Aqueous Wash in Printed Circuit Board Manufacturing
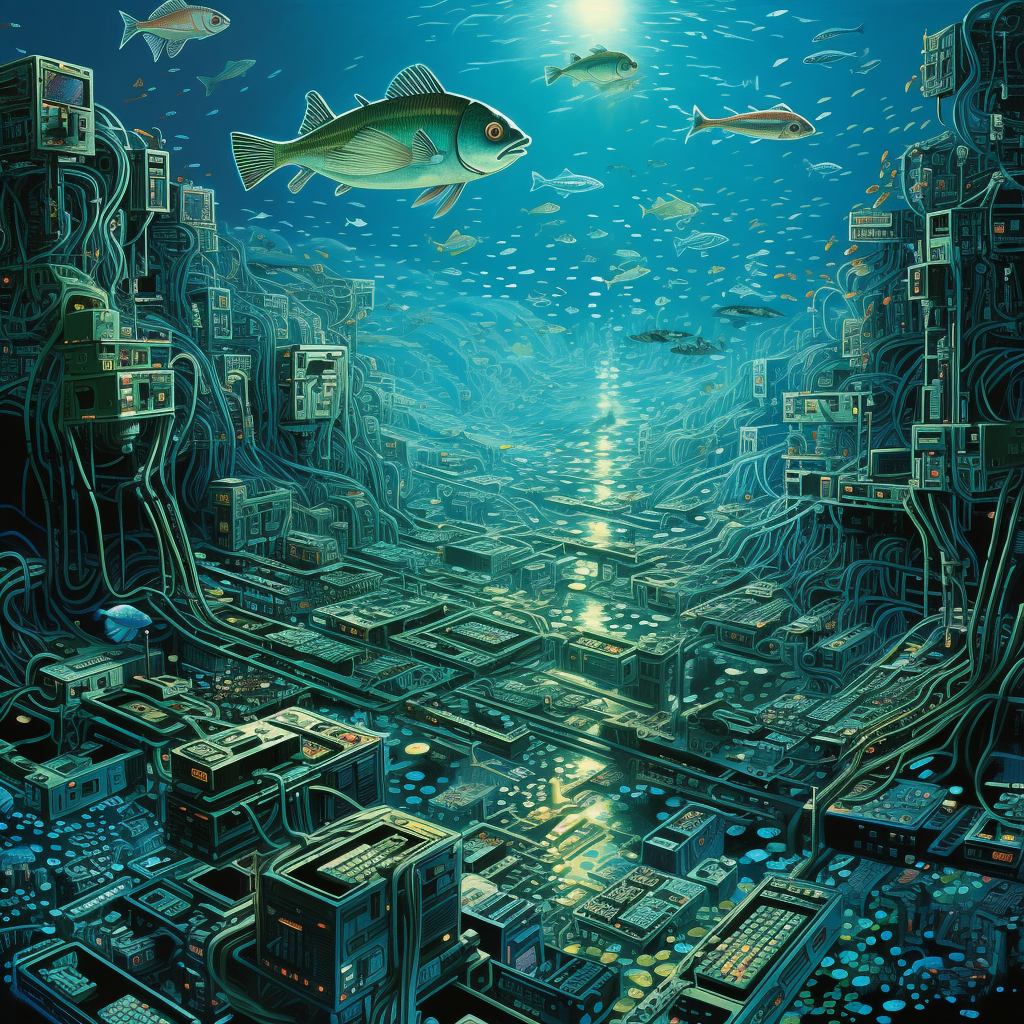
Printed circuit boards must be cleaned before testing. This imposes several design and build plan constraints that engineers must resolve. As PCBs become more crowded due to the shrinking size of components, engineers must select solvents or other cleaning solutions that can adequately penetrate tight spaces with fine pitch leads and low stand-off height. Additionally, consideration must be made for removing dissolved contaminants and suspended particulates.
If water is used in the aqueous wash process, it must be of sufficient purity to not leave residual salts or contaminants behind. Even with wash-free flux, significant contamination will still be present on a PCB following production. Pressurized washes are required to dislodge solder balls physically. Surfactants improve accessibility to tight areas by dislodging residue and suspending it within the solution. Saponifiers react with rosins to dissolve them for easy removal.
Manufacturing engineers should avoid the use of hazardous cleaning materials whenever possible. Additionally, highly flammable solvents impose a unique safety hazard that should not be discounted. Wave soldering should not be performed in areas that utilize highly volatile solvents to prevent the ignition of the solvent from stray molten metal.
Chlorinated Fluorocarbons may be used for vapor phase cleaning to dissolve non-ionic residue. Vapor phase cleaning allows for complete penetration of all non-sealed components on the PCB. Chlorinated Fluorocarbons require reclamation to prevent environmental release, significantly increasing tooling costs. Hydrofluorocarbons do not have the same environmental risks as CFCs. However, HFCs present a risk of accelerated corrosion in certain light metals. Perfluorocarbons may also be an acceptable alternative to CFCs. VOC regulations frequently omit perfluorocarbons due to relatively low toxicity; however, reduced efficacy makes it useful primarily in niche particulate removal.
Other chlorinated solvents have shown significant use for removing non-ionic materials; however, ionic residue removal is not recommended with this class of solvent. Short-chain alcohols such as isopropyl alcohol have an excellent record for dissolving ionic and non-ionic residues. Isopropyl alcohol is both toxic and explosive; however, it is the most widely used spray wash. The combination of chlorinated solvents and alcohol has produced excellent results in vapor-phase cleaning. Both azeotropes and zeotropes have shown high efficacy for ionic residue removal.
Wash solutions are under continual development as environmental stewardship and cost consciousness drive the industry to find better solutions. Volatile Silicon solvents have recently been suggested as an acceptable non-ionic residue removal method. Supercritical carbon dioxide has excellent penetrating capability in cleaning small, intricate boards. Carbon dioxide snow has shown promise as an abrasive cleaning medium. This snow ablation technique is popular due to the lack of residue left behind after evaporation. Plasma arc cleaning is a technology under development where electrical discharge into gas produces plasma which sears away surface contamination. Laser ablation has been used to a similar effect. Ultimately, both design and manufacturing engineers must work together to ensure the correct cleaning solution is used for the required application.
References:
Cohen, A., 2015, Prototype to Product: A Practical Guide for Getting to Market, Reilly, Boston, USA.
Shina, S., 2008, Green Electronics Design and Manufacturing: Implementing Lead-Free and RoHS-Compliant Global Products, McGraw-Hill, New York, USA.
Cala, F., Winston, A., 1996, Handbook of Aqueous Cleaning Technology for Electronic Assemblies, Electrochemical Publications LTD, Isle of Man, British Isles.
Member discussion