What is a House of Quality for Manufacturing?
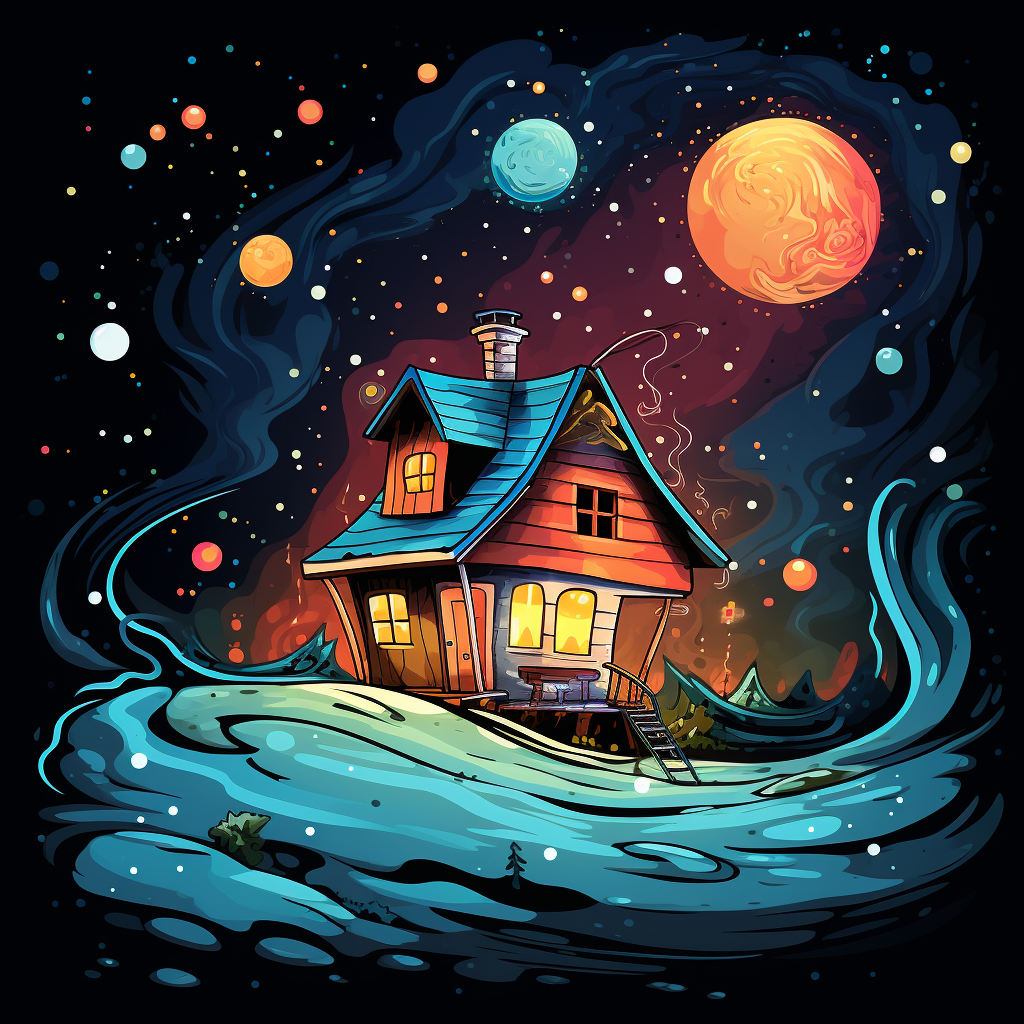
Hauser and Clausing wrote about the concept of a "House of Quality" customer requirements elaborating and ranking methodology in 1988. This grid-based ranking system allows for defining engineering requirements in the context of customer desires. As customer requirements may not always be clearly defined, they must be established as explicit requirements rather than vague notions of desire.
With the shift towards centralized manufacturing, customer requirements have become isolated from the teams that define the product [1]. As a result, customer requirements are frequently unmet due to engineers being unaware of the actual product requirements. Since unmet customer requirements fail to meet sales projections, it can thus be seen that eliminating the gap between customer requirements and engineering requirements is of paramount concern.
Quality Function Deployment is a method used to combat this growing gap. Pahl and Beitz write that the House of Quality methodology is the primary driving force behind QFD [2]. A House of Quality is a matrix created using particular criteria for each cell. This chart uses a general house shape to organize requirement data and rankings.
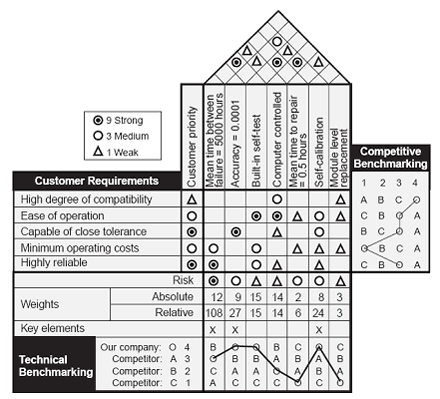
The walls of the house are composed of customer requirements. These indicate what the customer is looking for in the product. These requirements are general statements describing things the product should or should not do. Customer requirements are not stated in the context of engineering requirements or specifications at this stage.
The upper story of the House of Quality matrix is made of the engineering requirements. These are defined features of a product rather than customer-derived requests. Engineering requirements are measurable attributes that exist within a hypothetical product.
The roof of a House of Quality is composed of the interrelationship between each engineering requirement. Interrelationships are typically defined as strong positive, weak positive, no relationship, weak negative, and strong negative relationships. This allows engineers to determine which engineering requirements are aligned and which are contradictory. For example, increasing the strength of a structural member by thickening it has a negative relationship with the product being lightweight. An example of a strong positive relationship would be measuring a gasket's desirable flatness while defining the overall desirable thinness of a mating surface interface.
The basement of a House of Quality is the actual measurement of the associated engineering requirement. These are given weighted values to track against competing options. These target values may also be benchmarked against competitors [1 2]. As a result, the product under development will be designed in such a way as to have a greater chance of gaining market traction.
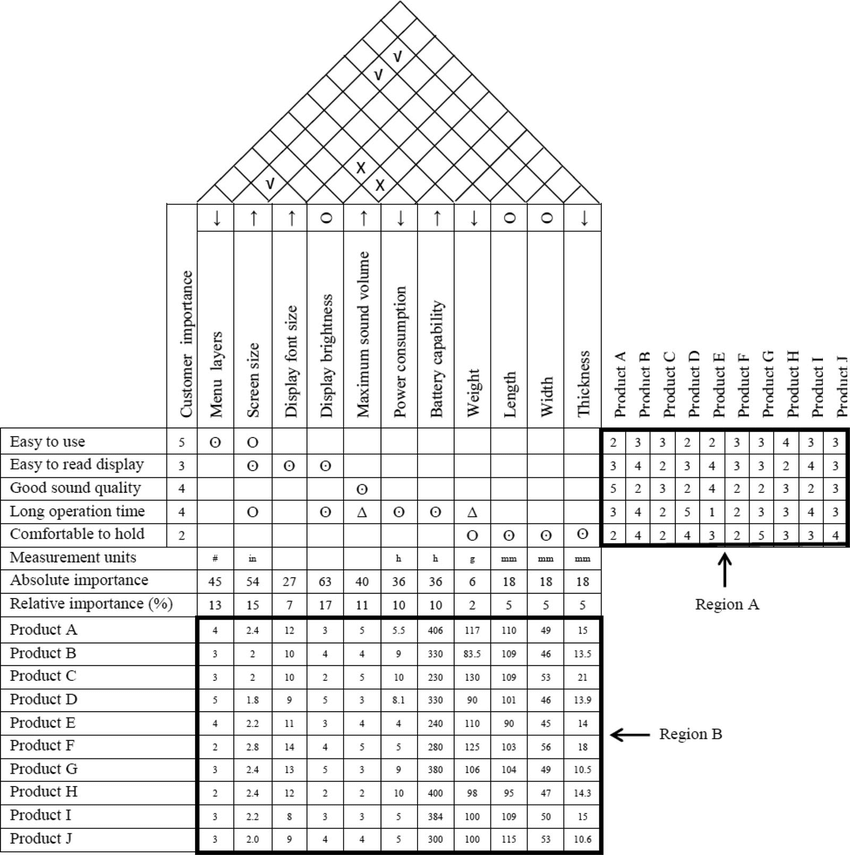
The primary motive driving the House of Quality is the center ranking feature [1]. These rankings may be performed in any desired way; however, the most common ranking is relative ranking. For example, the 1-3-9 method is prevalent. This method states that the most critical aspects are weighted to be about nine times as valuable as the least important aspects. Another method of ranking is absolute ranking [2]. This allows requirements to be ranked relative to each other, with a distinct preference for individual requirements close to others. A third method of ranking is binary ranking. This allows for simple "relative" vs. "irrelevant" ranking, drastically simplifying the final ranking calculation.
Patrick Brown wrote in 1991 that QFD yielded a distinct competitive advantage based on the improved focus on customer satisfaction, flowtime reduction, and generally enhanced product performance [3]. Quality Function Deployment focuses on "giving the customer a voice [3]." Through establishing the House of Quality matrix, customer desires are ranked based on customer importance and engineering necessity.
The House of Quality framework may be expanded to other areas. Using the same process, engineers may utilize the House of Quality technique to determine part configuration by importing the engineering characteristics from the previous House of Quality stage. Next, process planning may be accomplished by importing the part characteristics of the prior step. Finally, the product's requirements may be determined by importing the process operations from before [1].
Reference:
[1] Hauser, J. and Clausing, D., 1988, "The House of Quality," Harvard Business Review, May/June pp. 63-73.
[2] Pahl, G., Beitz, W., Feldhusen, J., Grote, K., 2007, Engineering Design: A Systematic Approach, 3rd ed., Springer Science & Business Media, London.
[3] Brown, P., 1991, "QFD: Echoing the Voice of the Customer," AT&T Technical Journal, Naperville, Illinois.
Member discussion