Design for Manufacturing: Machining Tapers and Contours
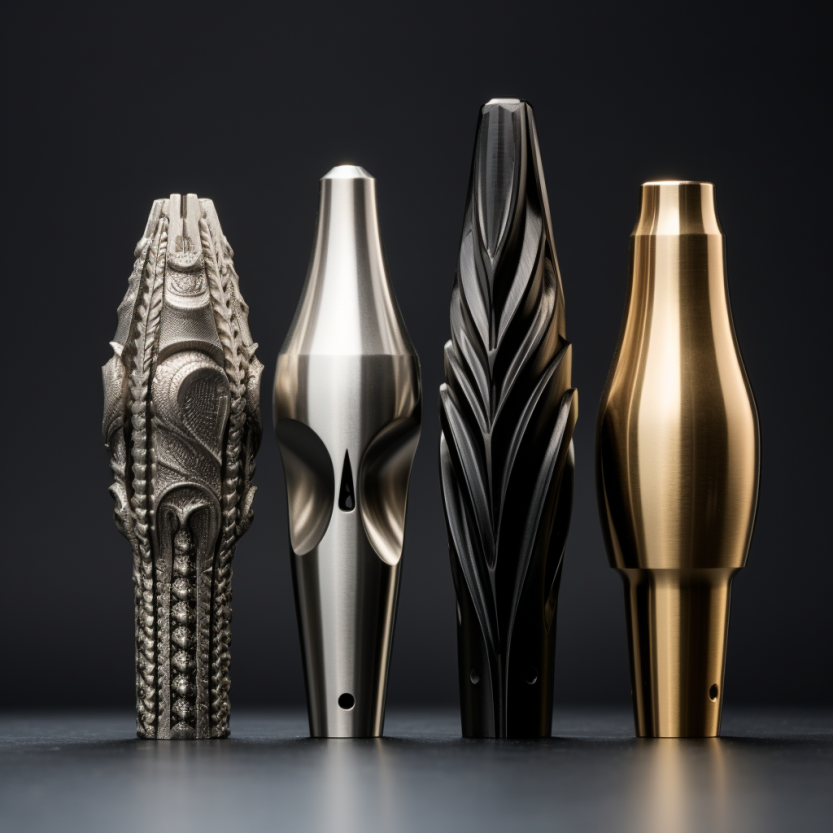
Manufacturing of machined goods often involves the creation of unconventional shapes. These unconventional shapes may require the use of specialized tooling. Design engineers should always consider the impact of specialized tooling on the overall tooling cost associated with a new product.
Tapers are machined parts that get thinner towards one end. Note how the above shape tapers off. The term may either apply to a tool or a part that is machined in such a way as to fit that definition. This rule deals with machining products to have a narrower end when compared to the other end along the part axis. To accomplish this machining, the workpiece must first be placed on a lathe. A trained machinist must then shave off material to reach a certain angle. This is difficult to accomplish by hand and may require computer numerically controlled machinery. CNC machinery is expensive and will substantially drive up tooling costs.
Contours are splines or curves applied to a three-dimensional machined part. Note the above curves on the shape. Contours almost always require CNC machinery to create with any amount of dimensional tolerance adherence. This will also increase tooling costs as trained operators must be paid. In addition, numerical control recipes must be created and loaded into the tooling. Whenever creating any design, avoid the use of undercuts unless necessary. The part shown above exemplifies all four key points not being followed.
Key Points:
(a) Avoid the use of tapers
(b) Avoid the use of machined contours. Use casting when possible.
(c) Preferentially design for rectangular shapes which allow for simple tooling
(d) Avoid the use of undercuts unless necessary
By following design for manufacturing guidelines, you can avoid making unnecessarily costly tooling decisions.
Member discussion