How to Perform Detailed Manufacturing Analysis of Tungsten Carbide Jewelry
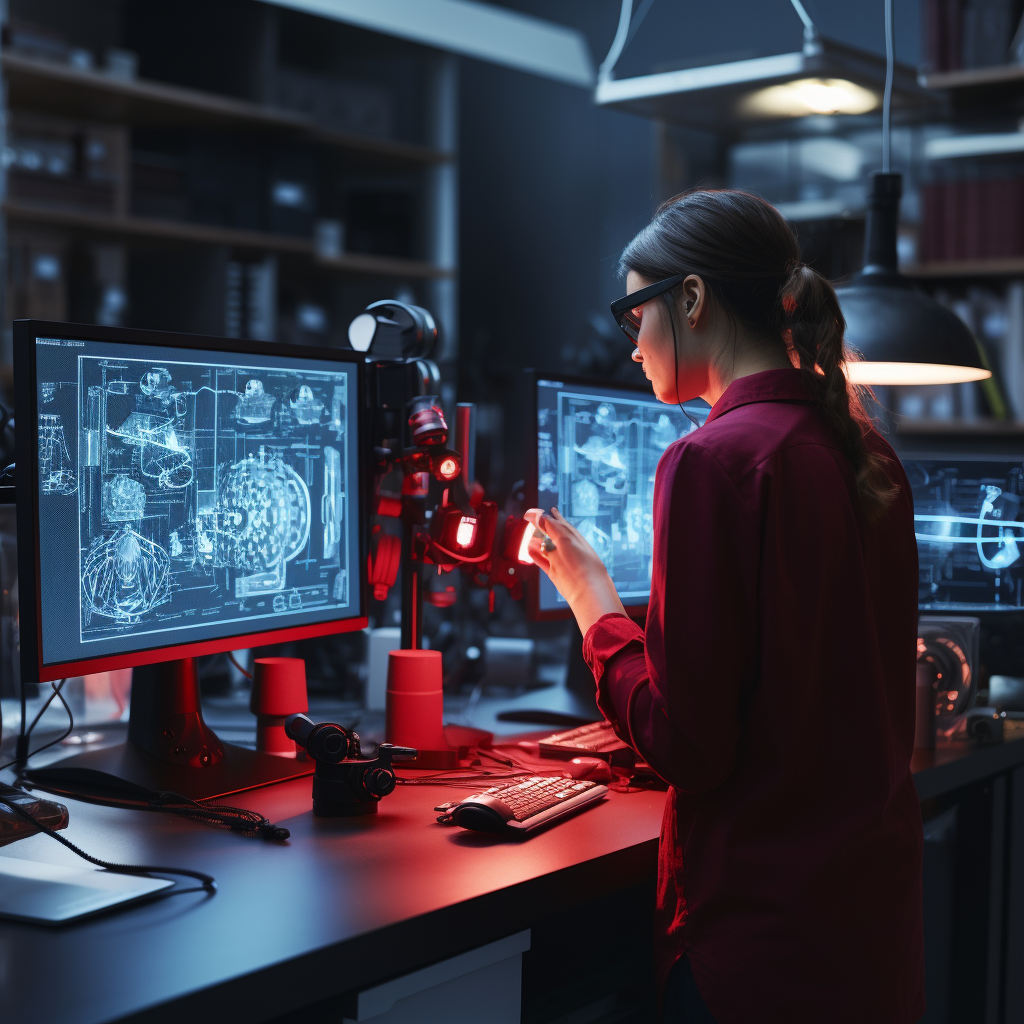
Tungsten carbide is one of the strongest alloys available for jewelry. Tungsten carbide wedding bands are popular due to their high resistance to scratching and low replacement cost in the event of being lost. These bands are cast via investment casting. Visual and computer representations are shown below.
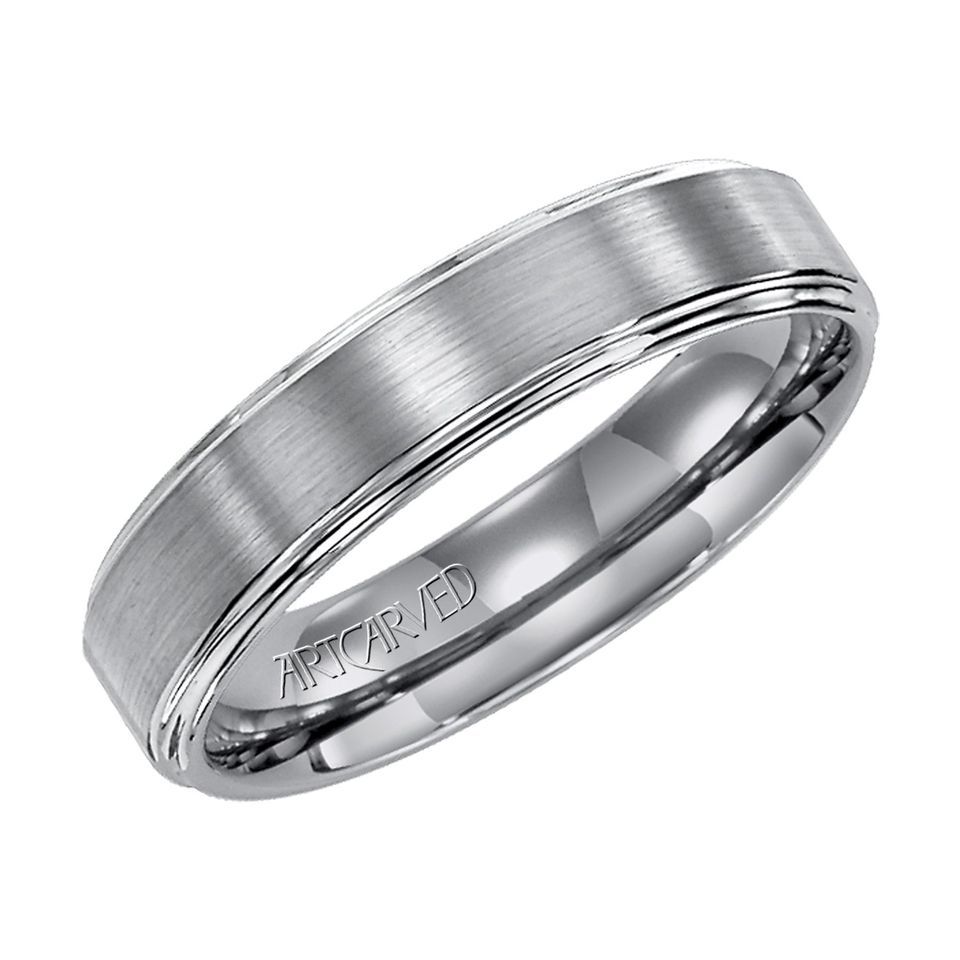
Based on part geometry, the ring is considered flat.
We can build a model in CATIA using a few basic part features.
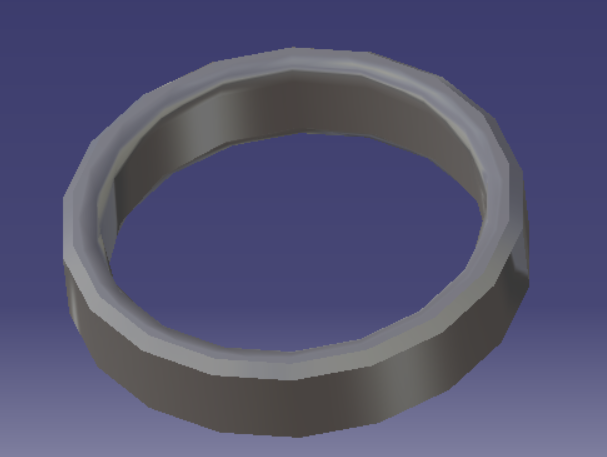
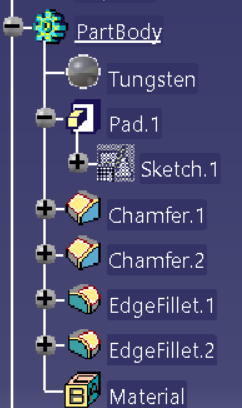
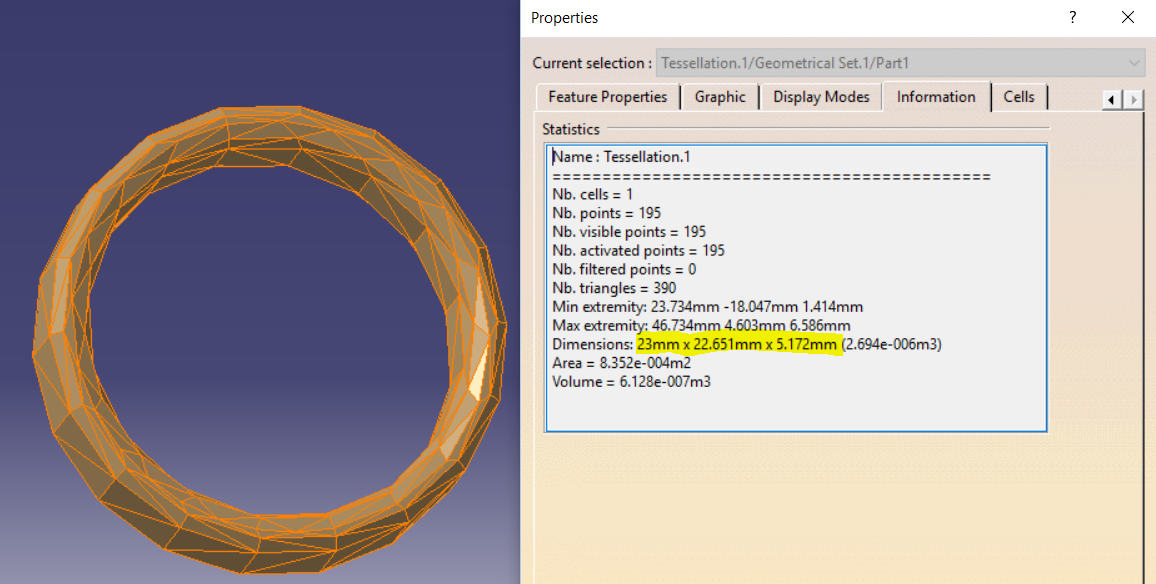
We can then perform a tessellation mesh extraction to obtain the volumetric data for the part body we made above.
The below tables provide information on calculating the relative die cost. For the purposes of the analysis, the ring is considered to be formed from an external mold and an internal mold with the chamfers being included in the molds. No special core is required. The chamfers do not meet the criteria for being an undercut. All tables are taken from the Poli textbook [1]. The surface finish is assumed to be negligible as it may be polished later. The surface finish is assumed to be 1.
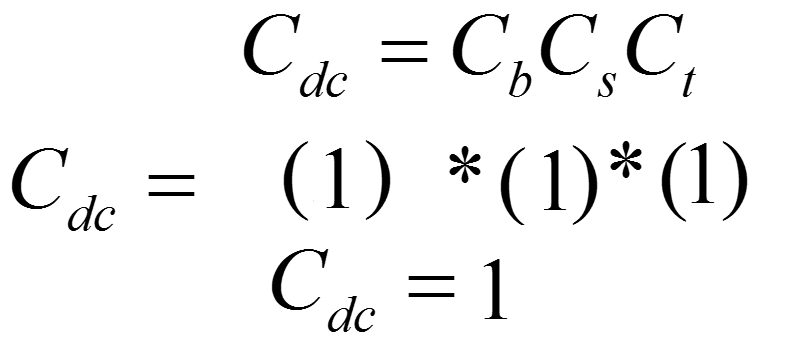
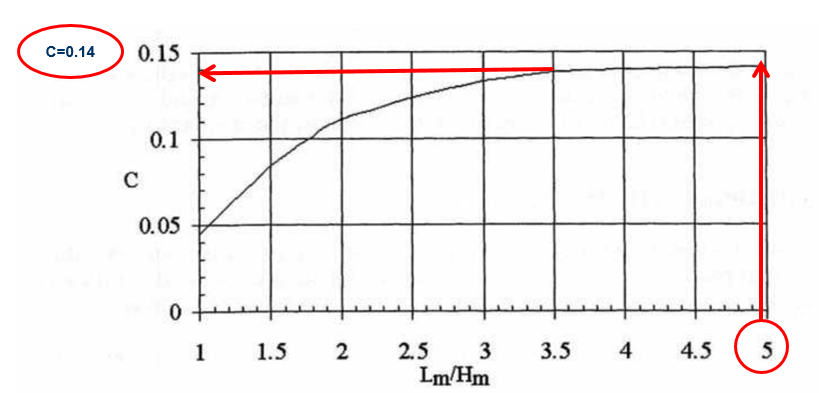
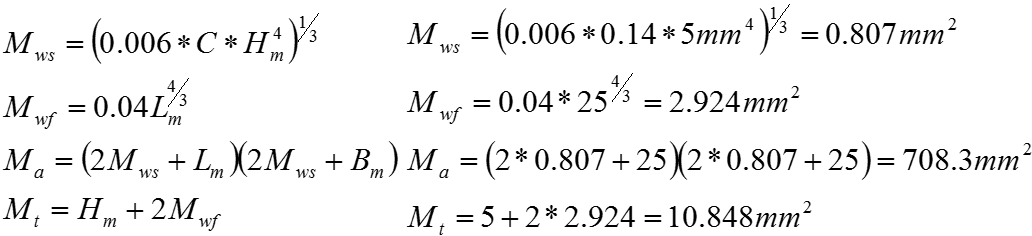
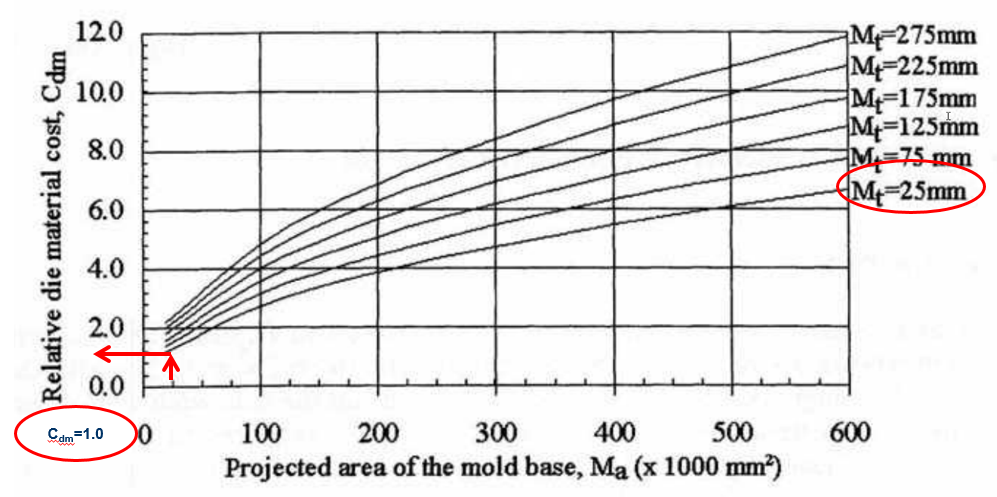
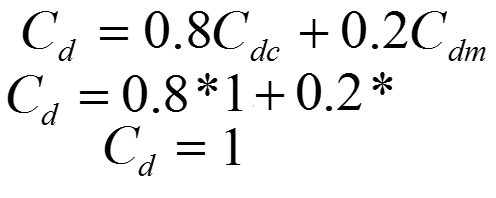
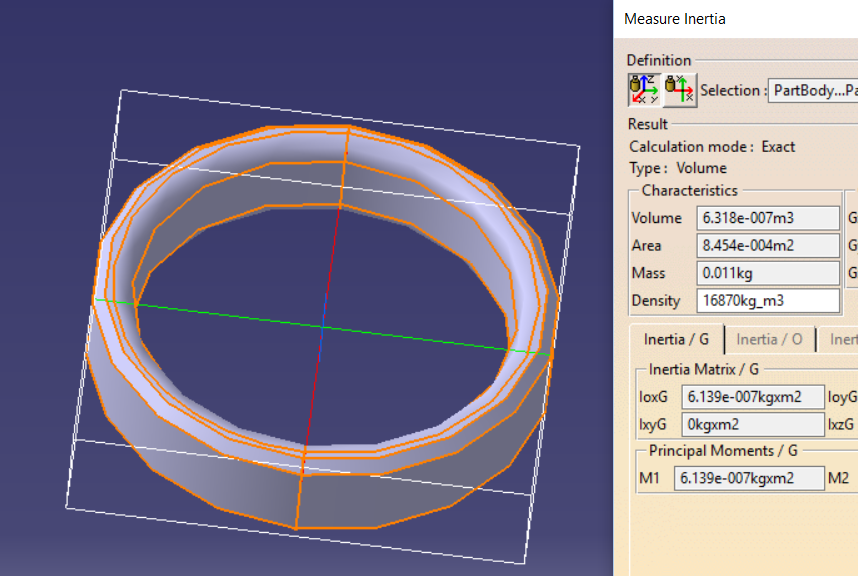
CATIA offers a suite of tools to calculate the volume of a part. The volume of the ring is 63.18um^3 and the volume of the reference part is 1.244um^3. Assuming 17$/kg for tungsten-carbide and 1.6$/kg for aluminum (as of 6/14/2016 closing), the relative price is 10.625. Therefore, the relative material cost is (63.18/1.244)*10.625 = 539.62
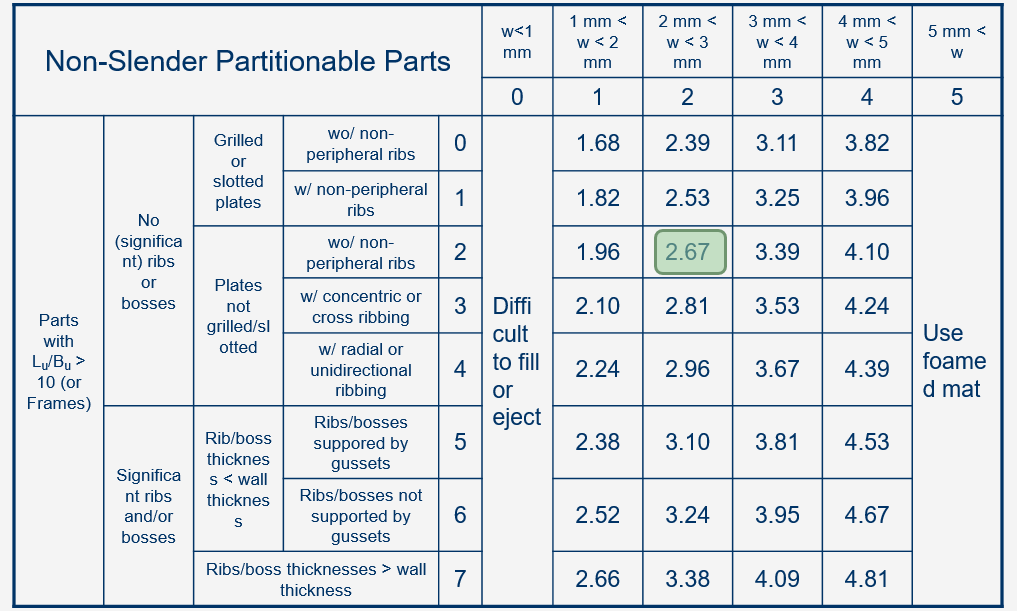
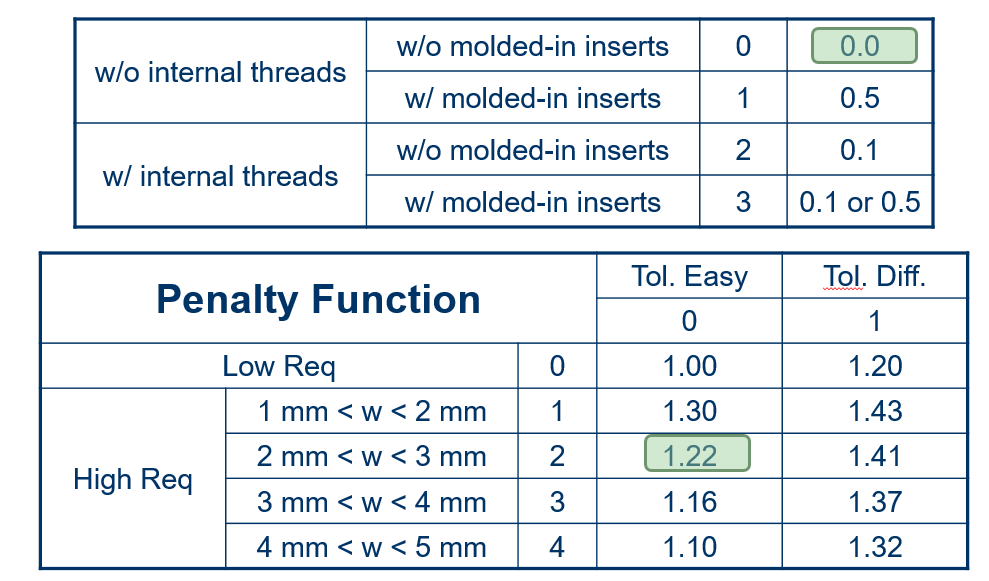
This gives us a relative time of (2.67+0)*1.22 = 3.2574
CATIA approximates the total area of the part projection at <1000 square mm. This results in the expected machine tonnage seen below.
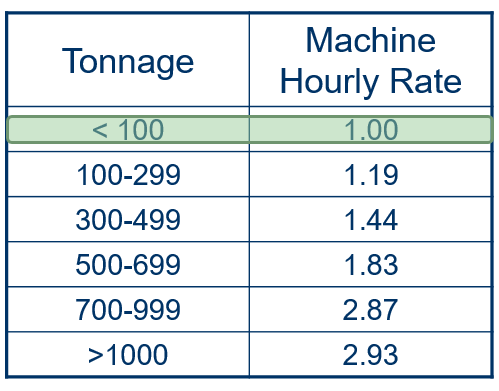
This results in a total relative processing cost of 3.2574.
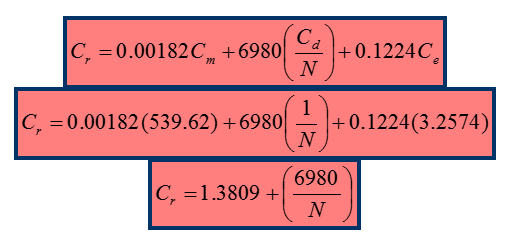
For 1000 units, the relative cost is 8.3609. For 1,000,000 units, the relative cost is 1.3879.
For this analysis, the surface finish results were not required to be calculated due to the ability of the machinist to perform finishing operations easily.
Relative material costs had to be calculated using spot prices retrieved from Metalprices.com [2].
Overall, die casting is closely related to injection molding from a design standpoint. Non-solid filler is expected to flow into a mold that is subjected to the same physical constraints shared between injection molding and die casting. This results in the same design tools being available to engineers performing both injection molding and die casting.
References:
[1] Poli, Corrado. (2001). Design for Manufacturing - A Structured Approach. Elsevier. Online version available at: http://app.knovel.com/hotlink/toc/id:kpDMASA001/design-manufacturing/design-manufacturing
[2] Metalprices.com, 2016, “MetalPrices.com – An Argus Media Service”, from www.metalprices.com.
Member discussion