Electron Beam Melting 3d Printing
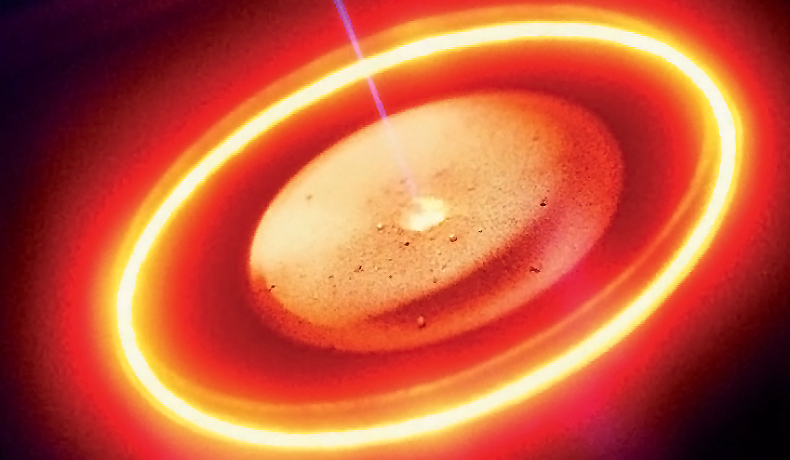
Electron beam melting is a similar process to selective laser melting. Electron beam melting differs from selective laser melting in that it is performed in a high vacuum. Due to the electron beam's higher energy density than a standard laser, full melt conditions are achieved in the material faster than under laser melt technology. As a result, electron beam melting produces finished parts at a higher rate than similar laser-based systems.
In an electron beam additive manufacturing system, the electron beam is generated by applying a 60kV potential and focusing electron movement into a collimated beam using a magnetic lensing system. The accelerated electrons are then steered into the desired scan pattern using an additional electromagnetic lens stage controlled by the toolpath code created from the CAD model in use.
After electron beam formation, the part being worked is painted with the electron beam to form melt pools. These pools allow for the complete liquid formation of the powder. After solidification, the beam generator is raised in the z direction, and fresh powder is raked onto the new top layer of the part. It is worth noting that due to the high vacuum, cooling of electron beam melted parts takes significantly longer.
The powder subject to EBM processing is typically preheated. This allows for the aggregation of the powder through a light sintering process. Preheating reduces thermal gradients during melting, allowing for a faster melt cycle with fewer induced thermal stresses. However, preheating has some impact on downstream processes that may be undesirable. Metallurgical bonds are formed in the powder during preheating, which may cause the powder to undergo uneven phase changes during the melting cycle.
A high vacuum is maintained in the build chamber for several reasons. As electrons are lightweight charged particles, collisions with gasses will result in electron beam diffusion. As molten metal pools are being formed, splatter may occur. Maintaining the build chamber in a vacuum prevents the ignition of reactive materials, which may be part of the workpiece. Additionally, the outgassing of chemically contaminated parts is promoted in a high vacuum state. This results in a more homogenous material with fewer contaminants after cooling.
Electron beam melting has shown promise in producing nickel-based super-alloy precision aerospace components. These components include jet engine compressor blading, engine nozzles, and space vehicle applications. This class of components requires low-density, high-strength components with excellent corrosion resistance in high-temperature conditions. Titanium aluminides have been demonstrated to be ideal candidates for these components. Electron beam melting has proven to meet the required specifications for microcrystalline structure formation while still being capable of producing highly complex parts.
Electron beam melting technology has been adapted to create high-strength permanent rare earth magnets. Nd2Fe14B magnets are particularly well suited to production using additive manufacturing. To create these magnets, the desired alloy is mixed and provided to the electron beam system as a powder. Because of the layer-by-layer production method, each layer beyond the first will naturally align magnetic domains during the liquid phase of the material. Current research is on producing rare earth magnet powders of a higher magnetic flux density.
Electron beam melting technology allows for high-quality material properties typically free of voids and relatively strong compared to other systems. EBM typically produces fairly tight tolerances and high-quality finishes as well. Despite this, electron beam melting still maintains a relatively fast manufacturing cycle.
Unfortunately, electron beam melting is constrained by the requirement to maintain a high vacuum in the build chamber. This adds to the cost of the system while also increasing the maintenance frequency. Electron beam melting has a relatively high power consumption which increases manufacturing costs. An added risk of electron beam melting is the spontaneous formation of gamma-ray radiation in the build chamber. This requires a tightly controlled vacuum chamber to protect personnel from radiation exposure.
References:
Chua, C., Leong, K., 2015, 3D Printing and Additive Manufacturing Principles and Applications, World Scientific, New Jersey, USA.
Srivatsan, T., Sudarshan, T., 2016, Additive Manufacturing: Innovations, Advances, and Applications, CRC Press, Boca Raton, FL, USA.
Murr, L., Gaytan, S., Ceylan, A., Martinez, E., Martinez, J., Hernandez, D., Machado, B., Ramirez, D., Medina, F., Collins, S., Wicker, R., 2010, "Characterization of Titanium Aluminide Alloy Components Fabricated by Additive Manufacturing Using Electron Beam Melting," Acta Materialia 58, 1887-1894.
Biamino, S., Penna, A., Ackelid, U., Sabbadini, S., Tassa, O., Fino, P., Pavese, M., Gennaro, P., Badini, C., 2011, "Electron Beam Melting of Ti-48Al-2Cr-2Nb Alloy: Microstructure and Mechanical Properties Investigation," Intermetallics, 19, 776-781.
Murr, L., Gaytan, S., Ramirez, D., Martinez, E., Hernandez, J., Amato, K., Shindo, P., Medina, F., Wicker, R., 2012, "Metal Fabrication by Additive Manufacturing Using Laser and Electron Beam Melting Technologies," Journal of Materials Science Technology, 28:1, 1-14.
Member discussion