Design for Manufacturing: Knurling
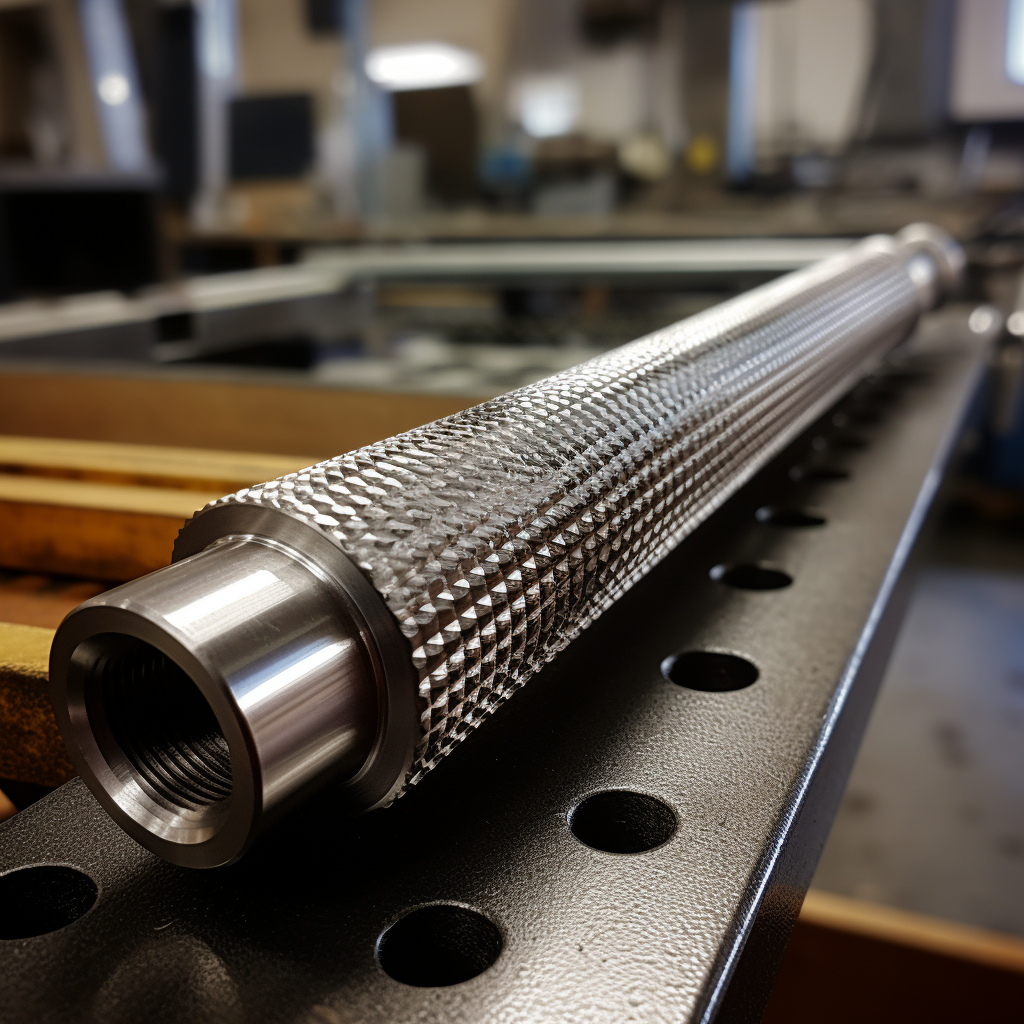
Knurling is the process by which repeated patterns are cut or rolled onto a material. Normally this is accomplished on a lathe or a rolling machine. Knurling is most commonly used to allow the end-user of a product to have an improved grip on the product by creating indentations on a smooth surface.
Knurling may also deform a part to correct a deviation from the design intent. In the event of a smooth-bore cylinder that has been warped, knurling may sometimes be used to expand portions of the cylinder to fit in the receiver. This process has fallen out of common practice with modern high-tolerance systems.
In the event of a smooth-bore cylinder that has been warped, knurling may sometimes be used to expand portions of the cylinder to fit in the receiver. This process has fallen out of common practice with modern high-tolerance systems.
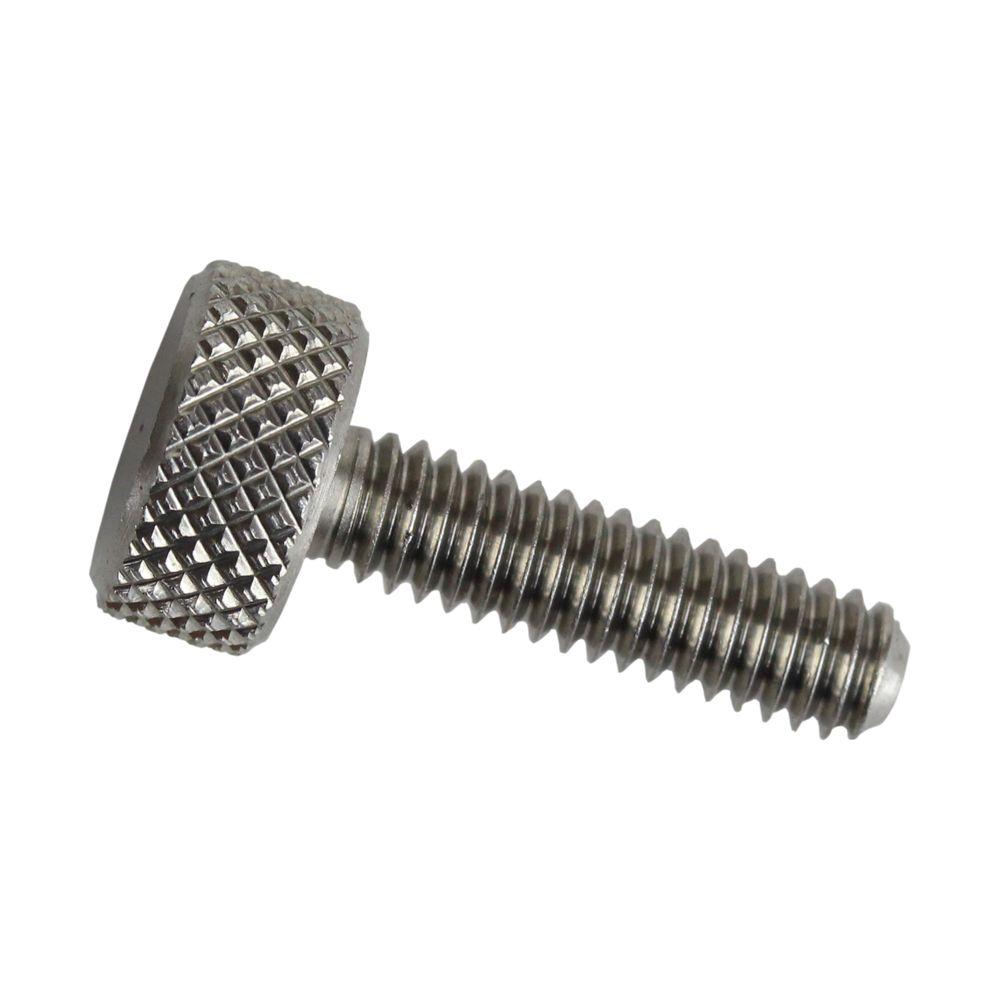
Sometimes, press-fit features may be created by creating a knurled surface. This allows for a part to be inserted so that it is retained by friction from the regular surface protrusions found on the knurled part.
Along the same lines, screw threads may be produced similarly to knurls. Ideally, screw threads will be rolled on using the same process as knurling. If this is not accomplished, screw threads must be cut in, which significantly increases both the cost and the chance of burring.
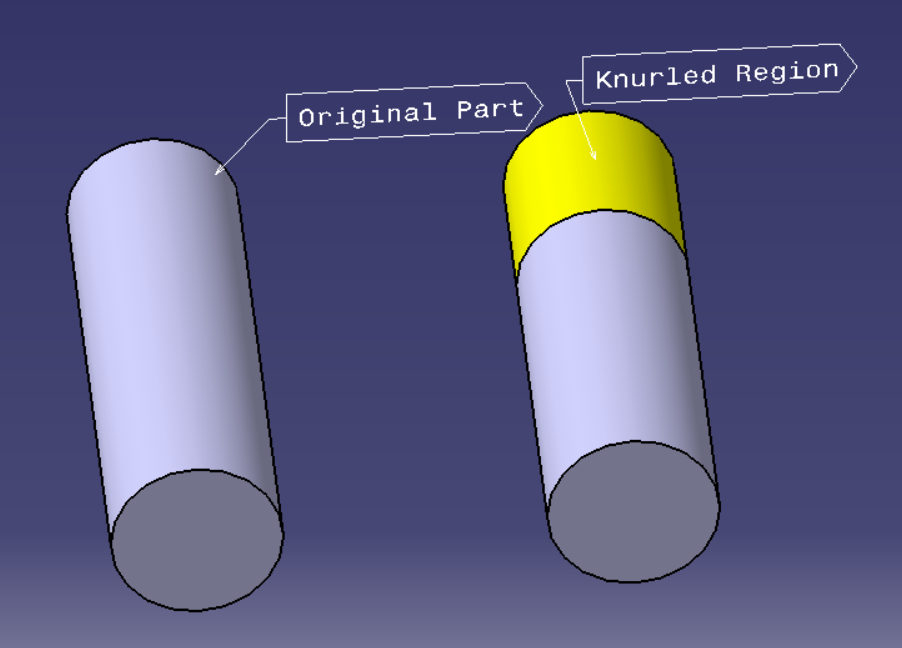
To ensure satisfactory knurl application, knurl band thickness should not extend beyond one full diameter of the rolled part. This ensures that sufficient force concentration exists to implement a satisfactory result. In addition to ensuring a satisfactory end product, costs may be reduced by preventing excessive tolerance requirements in the knurled area.
Design engineers should avoid excessive tolerance specifications. Knurls should be specified according to function and general density, as knurling is an inexact process. Excessive tolerance requirements will significantly increase both tooling and processing costs.
If
While designing parts that are to be machined:
(a) If knurling will be used
(b) Or if screw thread rolling will be used
Then
(a) Ensure that the width of a knurled area does not exceed the diameter of the part
(b) Specify the teeth in the knurl as a function of general distribution density or general size
(c) Specify the teeth in the knurl in terms of purpose (finger grip, appearance, or press fit) instead of tolerance
(d) Use rolling to create screw threads vice cutting to prevent burring
Adherence to this rule will prevent insufficiently knurled products from being created. Additionally, screw thread burring will be minimized, which both decreases production flow time as well as increases end-product quality.
Member discussion