Selective Laser Melting Additive Manufacturing
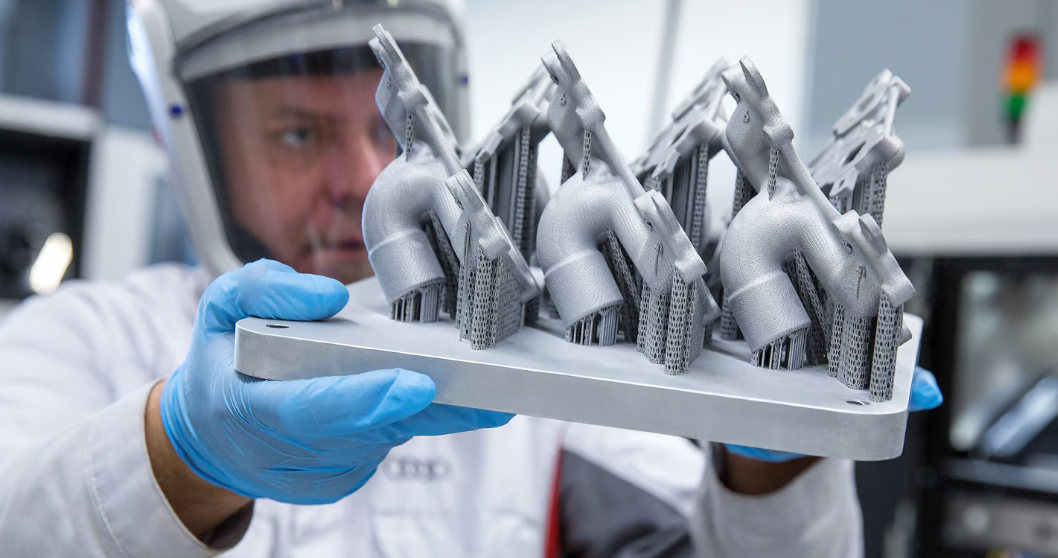
Selective laser melting (SLM) is a relatively new technology used to form metal products by applying a laser beam to a powder bed. This allows for various material and crystalline structure arrangements that are impossible with traditional manufacturing processes.
Laser melting is similar to direct metal laser sintering, except for complete melting in the powder bed. Rather than creating a semi-solid slurry, complete liquidification of powder occurs. This promotes a higher-density part which results in improved strength and durability. Laser melting-produced parts typically have improved surface smoothness and more homogenous microstructure patterns [1].
In addition to improved structural performance, selective laser melting processes require fewer post-processing steps when compared to direct metal laser sintering. Eliminating post-processing stages causes a higher overall production rate, reduced labor costs, and a less expensive end product. Unfortunately, the disadvantages sometimes nullify the advantages of laser melt additive manufacturing. Due to slurry formation, highly viscous nonferrous metals frequently suffer from balling, which may be exacerbated in some applications of selective laser melting [2].
Balling is the phenomenon by which small spheres or ellipsoids of metal between 10 and 500 micrometers form during laser sintering and melt processes. This process is accelerated by oxygen contamination of the atmosphere. Balling both increases surface roughness and causes increased porosity of the finished product. This results in a weakened structure due to void formations. In particularly severe balling scenarios, the automatic wiper blade may have its motion impeded by ball formation, resulting in total print failure.
In some cases, the physical processes causing balling are understood. In the case of ball formation of around 10 micrometers, it has been determined to be the result of insufficient incident thermal energy applied to the powder bed. In the case of more extensive ball formation, splashing in the molten pool formed under high scan speed conditions is suspected to be the cause.
Other researchers disagree because capillary instability may cause balling under many conditions. Simchi and Pohl published a study stating that scan line spacing reduction may reduce laser melt balling in a study where specific energy output, scanning rates, scan line thickness, layer thickness, scanning geometry, and atmospheric constituents were studied [3]. Simchi and Pohl's study primarily dealt with partial melt scenarios in ferrous material melting, so the results cannot be seen as conclusively applicable to nonferrous complete melt processes. Additional studies involving varying atmospheric gas concentrations, layer thicknesses, and actual statistical modeling of balling impact on the overall SLM process are areas of future study.
In addition to balling, molten pool instability contributes to selective laser melt failures. The liquid-solid transition zone tends to experience material shrinkage due to phase transition. As a result, warping of the end product may occur. Additionally, severe material shrinkage may result in complete delamination between the print layers resulting in total part failure on the print bed. Due to residual stress formation, tearing, and crack formation have also been observed in copper alloyed materials. Future laser and powder selection studies may reduce these risks [1].
As of 2009, selective laser melting has entered the dental field for individually customized dental appliances. Dental-field SLM systems typically employ relatively low-power lasers of approximately 100W. Generally, applications in the dental industry see the use of only a few select alloyed materials. Most alloys are Titanium based due to the high biocompatibility of the material. The majority of dental appliances created are bridges and crowns. Additive manufacturing is gradually displacing casting and CNC milling as the preferred method of dental appliance creation as dimensional tolerances matching and accuracy continue to improve [4].
Another area of research in selective laser melting is the creation of exotic alloys. Elemental particles may be added to existing alloy powders to create otherwise impossible-to-produce materials. Ceramic-metal hybrid alloys are a specific area of research where laser melt technology is required. Ceramic particles are homogeneously mixed throughout a metal powder matrix and subjected to high-temperature laser melting.
Additional alloying powders may be added during production to achieve desired mechanical properties. For example, Silicon is added to reduce crack formation in Al7075 hybrid alloys. Research is ongoing in these areas as the underlying principles behind these material property changes are not always well understood [5].
Selective laser melting typically produces high-quality parts with excellent mechanical properties. Similar to direct metal laser sintering, a vast array of materials is possible so long as it may be processed into a powder. Selective laser melting allows for fast, low-cost solutions due to the lack of post-processing required compared to other systems (including laser sintering). Compared to other available technologies, highly complex, accurate parts are possible through SLM systems.
Selective laser melting suffers from many of the same disadvantages as laser sintering. SLM systems are both large and typically require a large amount of power. Selective laser melting is a relatively slow process when compared to traditional machining. Despite a relatively fast build rate compared to other AM processes, SLM still lags behind mills and lathes in product creation speed [6].
References:
[1] Gu D., Meiners, W., Wissenbach, K., 2012, Laser Additive Manufacturing of Metallic Components: Materials, Processes, and Mechanisms, International Materials Reviews, 57:3, 133-164.
[2] Li, R., Liu, J., Shi, Y., Wang, L., 2012, Balling Behavior of Stainless Steel and Nickel Powder During Selective Laser Melting Process, International Journal of Advanced Manufacturing Technology, 59: 1025-1035.
[3] Simchi, A., Pohl, H., 2003, “Effects of Laser Sintering Processing Parameters on the Microstructure and Densification of Iron Powder, Materials Science Engineering A, 359(1-2):119-128.
[4] Gebhardt, A., Schmidt, F., Hotter, J., Sokalla, W., Sokalla, P., 2010, Additive Manufacturing by Selective Laser Melting: The Realizer Desktop Machine and Its Application for the Dental Industry, Physics Procedia 5, 543-549.
[5] Srivatsan, T., Sudarshan, T., 2016, Additive Manufacturing: Innovations, Advances, and Applications, CRC Press, Boca Raton, FL, USA.
[6] Chua, C., Leong, K., 2015, 3D Printing and Additive Manufacturing Principles and Applications, World Scientific, New Jersey, USA.
Member discussion