Review of Pahl and Beitz on Conceptual Design
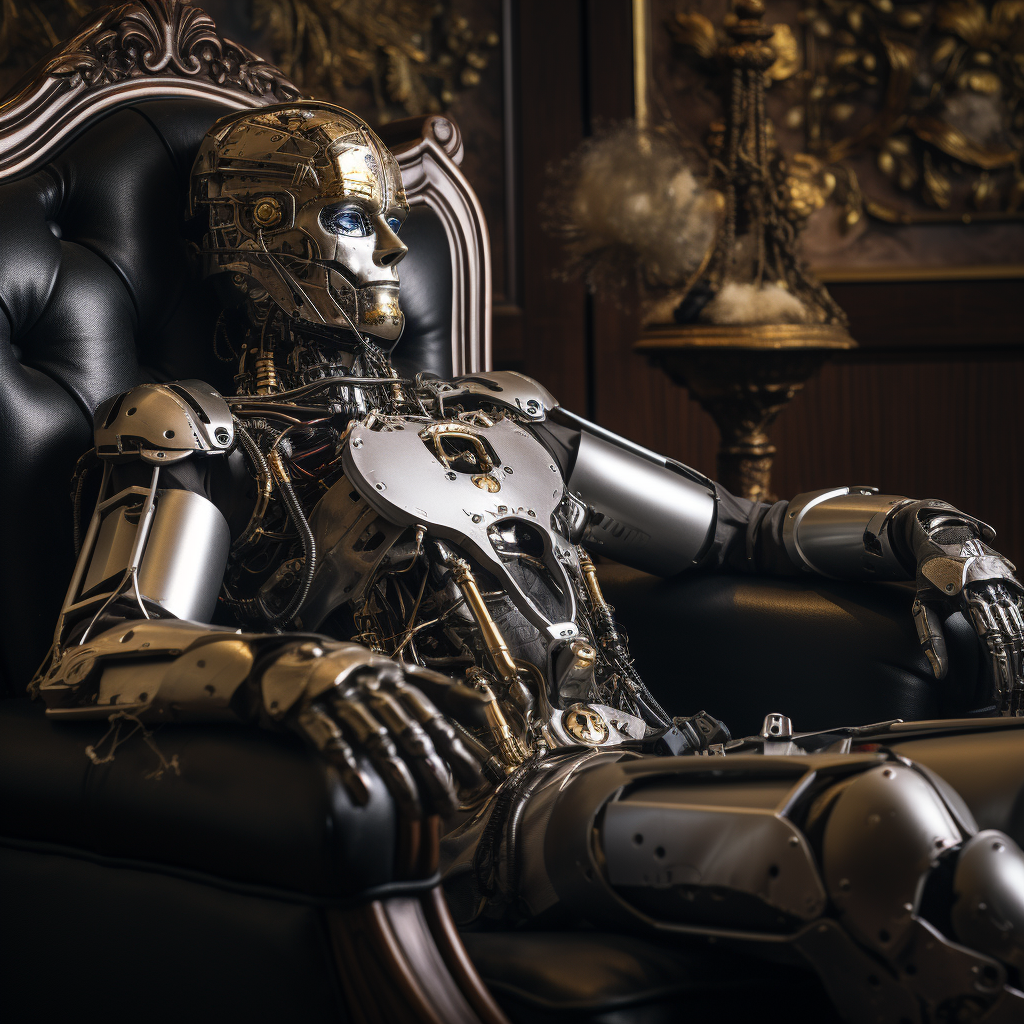
Pahl and Beitz treat conceptual design as the first stage of the systematic design process [1]. This stage of design utilizes several principles in order to achieve a result that encapsulates the problem the product seeks to overcome. The conceptual design immediately follows the problem definition in the design process. The embodiment of the conceptual design occurs at the conclusion of this stage in the design process.
Conceptual design deals primarily with the abstraction of a proposed solution such that it is possible to define multiple solutions within the confines of the concept design. Specific measurements are not used nor are specific engineering requirements in this stage of development. Instead, defining goals related to the product should be the focus of the conceptual design.
Individual steps to achieve each goal may be elaborated upon during the conceptual design stage. For example, Pahl and Beitz suggest that the elaboration of methods to “reduce cost” should be explored if that is the overall goal of an adaptive or variant design [1]. However, specific steps to accomplish this should generally be avoided. Instead, broad steps to accomplish the product goal must be considered.
Pahl and Beitz provide a five-step process for creating an unbiased solution for a product to resolve a problem. The first step is to eliminate all personal preferences present in a selected design or solution. As individuals spend time and effort on particular solutions, they become biased toward that given solution. The second step is to omit requirements that do not match customer demands or engineering constraints. This may be accomplished using Quality Function Deployment tools such as the House of Quality. The third step is to convert qualitative requirements to quantitative requirements and then reference them to engineering requirements. This can also be assisted by using the full House of Quality system. Next, requirements produced in the previous step should be generalized to eliminate solution bias. Finally, the problem should be stated in terms that do not show bias to any particular solution.
A useful method to determine the broad steps required to achieve the overall product goal can be found in the functional modeling system. This system allows for generalized product solutions to be created without showing bias towards any particular solution. In order to create a functional model, the overall problem statement must be rewritten as an overall function for the problem. Next, this function should be broken down into component subfunctions. Each subfunction is then broken down into smaller subfunctions iteratively until the lowest-level solution is found. At this point, a functional model can be considered to be complete with the exception of flow.
The functional model flow must be considered to complete the model. Flow is defined as the transition of energy, signals, or material from one state to another. Typically, flow is defined in a verb-noun sequence using standard language such as that defined by Wood and Stone [2].
Solution criteria should be considered with regard to how it impacts the requirements list. This may be broken down into several primary headings such as function, safety, ergonomics, maintenance requirements, and costs. These evaluation criteria may be used in processes such as the House of Quality in order to drive engineering and customer requirement elaboration. These requirements may be related to the likelihood of accomplishment as well as the overall desirability for the customer.
Overall, the Pahl and Beitz methods demonstrated throughout the material have proven themselves to be particularly useful in concept elaboration. These techniques allow for both standardized and repeatable product functional design. Without a standardized structure to follow, design engineers will create different models for each product under review which may result in increased design flow between teams due to the inability to communicate on issues. By utilizing the methods suggested by Pahl and Beitz, engineers are able to reduce flow times and costs associated with design.
[1] Pahl, G., Beitz, W., Feldhusen, J., Grote, K., 2007, Engineering Design: A Systematic Approach, 3rd ed., Springer Science & Business Media, London.
[2] Stone, R. B. and Wood, K. L., 2000, "Development of a functional basis for design," Journal of Mechanical Design, Vol. 122, p. 359. - 370
Member discussion