Laser Stereolithography
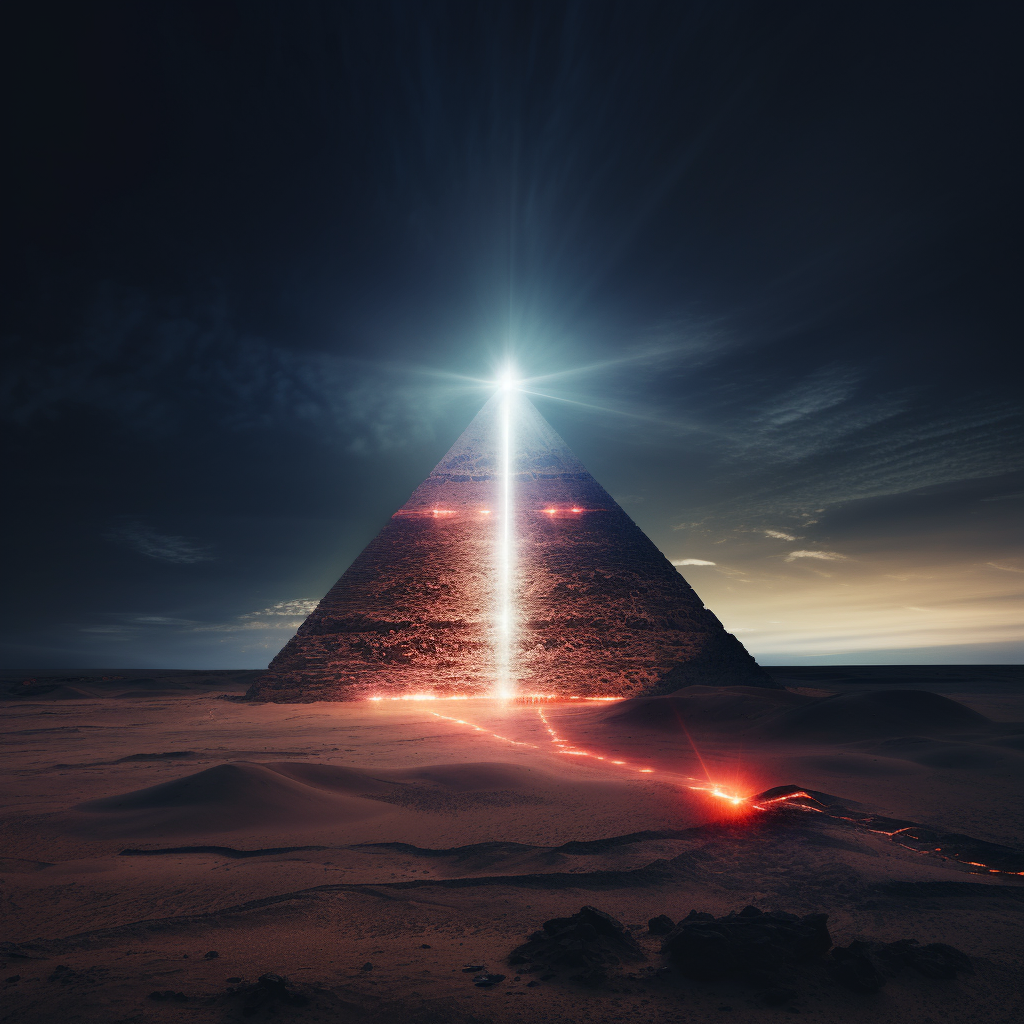
Stereo-lithography was one of the first additive manufacturing systems developed. In 1986, Charles Hull patented the first additive manufacturing device. This system linked monomer resin into polymer chains using ultraviolet wavelength photons. The original stereo-lithography systems were primarily used to create nonfunctional prototypes but were quickly expanded into functional products.
Modern stereo-lithography is an additive manufacturing process where ultraviolet lasers cure successive layers of a photo-reactive polymer. The UV laser is directed through an array of numerically controlled mirrors. As the laser moves across a vat of liquid resin, it cures a pattern that will become the finished product layer. The workpiece is then lowered deeper into the vat to allow another layer to be added to the top. Stereolithography 3d printers are becoming more accessible for home use as the technology is refined.
Stereo-lithography required particular data, which was first consolidated in a file type known as a STereoLithography file. This file described a 3d model in terms of the overall shape as seen through a triangular mesh. Each file would contain positional data for each triangle vertex with a vector normal to the resultant triangle to indicate the direction of infill for the shape. Over time, using STL files in additive manufacturing gradually created the Standard Triangle Language backronym.
Current research has yielded numerous types of photopolymers that are available for use in additive manufacturing. These photopolymers may be cured using gamma rays, X-rays, UV, visible range light, and electron beam forming. Despite this wide range of selection, the overwhelming majority of photopolymers in use still use ultraviolet light as the curing mechanism.
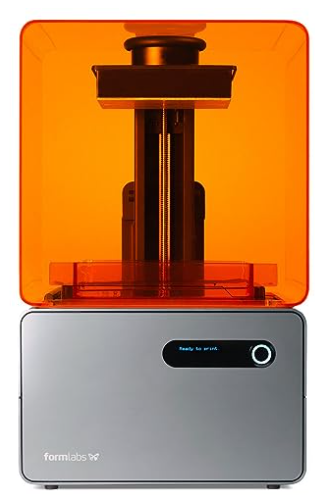
Polymerization is the term that describes a photopolymer being cured. This is an energetic process that is typically exothermic. Photo-initiator molecules in the uncured photopolymer are exposed to a photon source that excites them into becoming an initiator free radical to be used as an initial reagent in the polymerization reaction.
Initiator reagents act as catalysts to start the reaction. These initiator molecules react with monomers to form a polymerization-initiating molecule chain. These polymerization initiators will bind with other photopolymer molecules and subsequently create links. This continues until the polymerization initiation reaction is terminated chemically. As a result, long-chain polymers may be formed from a photo-reactive substance using photon exposure as the initiating mechanism. These long-chain polymers are bound together between layers as the workpiece is lowered deeper into the photo-vat, covered with fresh, uncured photopolymer, and exposed to UV light.
Other photopolymerization methods are also possible. Recent research has yielded photopolymers that operate using cationic initiators. This chemical mechanism produces epoxies formed by exciting iodonium or sulfonium salts. Unfortunately, this chemical mechanism requires more input energy which is accomplished using a higher-power UV laser. Cationic photopolymerization is preferable to traditional photopolymerization due to the stronger mechanical properties present in the fully formed products. This allows for a broader range of use for additive manufacturing produced parts.
Stereo-lithography is still widely used in additive manufacturing. Rather than only being used industrially and commercially, residential stereo-lithography 3d printers are now available for individuals wishing to create rapid resin-based prototypes. The costs of the printer systems and the resin have fallen dramatically with mass adoption, creating an economy of scale. Systems that previously would cost hundreds of thousands of dollars now have near-equivalent systems available for around two thousand dollars. Home models are available for a few hundred dollars.
Stereo-lithography maintains active use due to the advantage it offers over some newer technologies. As there is no high-power heat source, stereo-lithography photopolymerization can be accomplished continuously with little monitoring. Stereo-lithography allows for relatively large build volumes when compared to some other systems. Stereo-lithography also uses a wide variety of materials. This allows for numerous combinations of photopolymers resulting in many options to satisfy mechanical and thermal constraints. Finally, stereo-lithography allows for relatively high-quality surface finishes compared to other systems.
Stereo-lithography is not without faults. Stereo-lithography additive manufacturing requires support structures added to the build plan for undercuts and overhangs. Stereo-lithography also requires lengthy post-processing to produce a finished part. Some photopolymers also need post-curing, which further lengthens the build cycle.
Member discussion