Introduction to Additive Manufacturing and 3D Printing
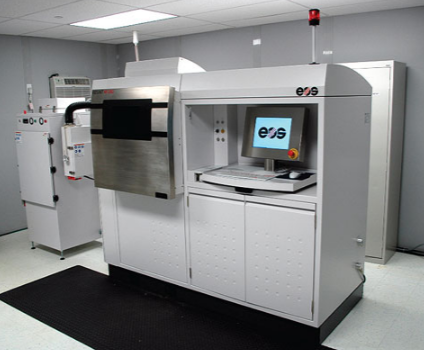
With the rise of additive manufacturing processes being utilized in rapid prototyping and low-volume production, it became necessary to develop technology to produce metal products. Laser sintering has existed since the 1980s; however, it took until the mid-1990s for this process to see significant adoption for use in additive manufacturing. There are now several branches of laser sintering-based additive manufacturing in everyday use. Laser sintering has been expanded to nonmetals and various metal alloys.
As these additive manufacturing processes become more refined, similar technologies have been developed along different lines. Electron beam additive manufacturing uses a focused electron beam as a heat source to fuse metal powder or wire together to form a product. As these two technologies have developed, companies in fields such as the medical appliance and aerospace industries have begun showing interest in full-scale production runs using these systems.
Materials produced via additive manufacturing (also called Material Incremental Manufacturing) are first created in a computer-aided drafting program like SolidWorks or CATIA. Special care must be given to ensure that the part conforms to the restrictions of the particular technology to be utilized. Additional consideration should be given to using the special features available to MIM, such as hollow shells, internal undercuts, and internal cavities. The product model to be created via AM is then tessellated and exported using the standard triangle language file format for use in developing the code for use with the additive manufacturing device.
STL files capture mesh data on the overall shape of the part, which is then imported into a toolpath generation program such as Repetier or CURA. Toolpaths are created for the MIM printer in the form of Gcode. This code will carry machine-specific data from deposition speeds to laser power levels. Gcode may be uploaded to the rapid prototyping device via Internet connectivity or SD card.
Initially, the creation of metal products through additive manufacturing processes was limited to the molds used in casting. Polymer and wax-based molds were printed using extrusion technologies, allowing for investment casting of a metal product. Investment casting is where disposable molds are created from a master mold. These disposable molds are then filled with molten metal. After the molten metal has solidified, the disposable mold is melted off the product. The product is then machined to achieve the desired surface finish and tolerances.
Technological advancement would see the introduction of focused energy systems such as laser and electron beam sintering and melting systems. As industry leaders recognized the potential advantages of such systems, greater research occurred in these areas. Present-day research is focused on optimizing relatively exotic alloys and applications of on-demand manufacturing in microgravity environments such as the International Space Station.
Laser stereo-lithography, laser beam, and electron beam additive manufacturing processes have rapidly advanced since their inception. These manufacturing processes have been improved from rapid prototyping to full-scale production systems for highly sophisticated parts. Resin curing through ultraviolet laser use allows for low-cost, lightweight prototype parts in a fraction of the time required through traditional manufacturing systems. The unique material structures possible through sintering and powder melting processes allow design engineers to construct designed alloy structures not possible through any other method.
Most ongoing research in these three technologies primarily involves enabling a more comprehensive array of materials for use in additive manufacturing. This research centers around the parameters required to produce usable parts for a given material. Over time, more exotic materials can be created using additive manufacturing.
Eventually, additive manufacturing will allow the creation of materials that are impossible using modern manufacturing systems. These future materials will likely involve exotic ceramics and element agents to obtain useful electrical, mechanical, thermal, and magnetic characteristics.
As optimization research continues, additional materials can be created using the methods outlined in this review. Eventually, future additive manufacturing advancements may allow for design-to-order materials to match desired physical properties for a given part or product. Instead of selecting materials to achieve desired physical characteristics, future advances may allow for precise tuning of chemicals to match all desired parameters for a given situation perfectly.
Member discussion