How is Poka-yoke Used in Fixture Design?
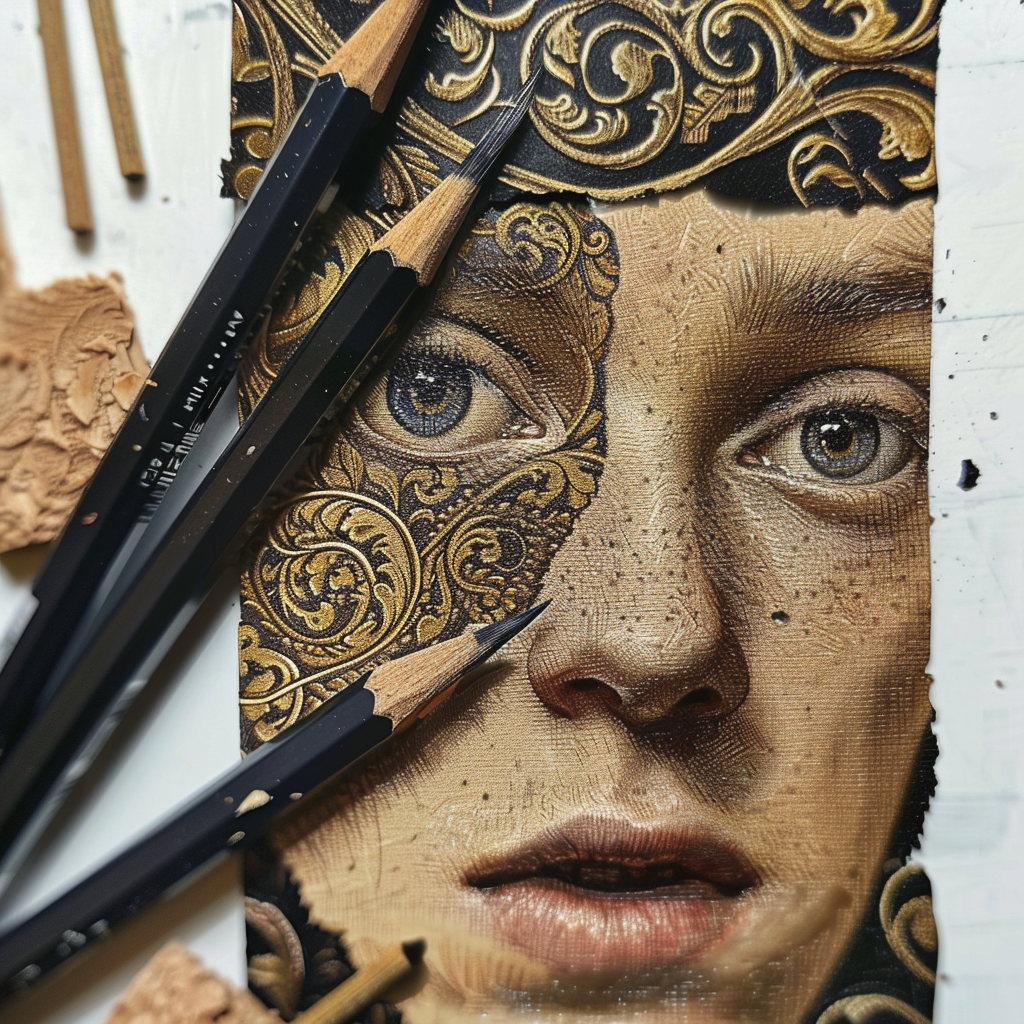
Poka-yoke, the process by which mistakes are engineered out of a design, is often incorporated into fixture design. Fixturing relies on restricting the movement of a workpiece in order to allow for proper machining. Fixtures enable engineers to bypass problems inherent with bad designs. Fixture design can be considered similar to poka-yoke practices in that excellent design decisions will result in fewer errors made by the assembly specialist.
Fixtures typically utilize clamps in order to constrain an object by one or more directions of translation or rotation. Poka-yoke may be incorporated in this through preventing the incorrect orientation of a workpiece. This type of error proofing prevents a distracted assembly worker from aligning a near-symmetric workpiece incorrectly. As a result, workflow is smoother as fewer decisions pertaining to handling must be considered by the assembly worker.
Fixtures also utilize locating pins in order to assist the assembly worker with workpiece processing. Locating pins involve poka-yoke concepts in that their usage may reduce or prevent errors associated with misalignment of parts. Selection of different locating pins may allow fewer product quality rejections due to greater range of motion of the workpiece in some directions when datum point tolerances along a certain plane are less strict. Through permissive and restrictive use of different locating pins, design engineers can increase production flow rate while still preventing misaligned parts.
Fixture supports are used to perform planar location of workpieces. These supports locate the workpiece in one axis. Supports may be either fixed or adjustable. Design engineers seeking to minimize the chance of misaligned parts may utilize poka-yoke error proofing to constrain fixture supports between particular ranges. Alternatively, design engineers may opt to use support sets in lieu of clamps to constrain the workpiece by multiple degrees of freedom in order to avoid potential stress damage from over-clamping. In this way, potential errors are engineered out of the design.
Another consideration for error-proofing in fixturing is to consider the impact of the cutter on the workpiece. As fixtures are used to hold pieces for machining, consideration must be given to the literal impact of the cutting edge against the material. This impact will create radial forces about the drilling axis which must be accounted for by the engineer designing the fixture. If proper care is not made to ensure that this force is either clamped or supported, the fixture may not work as intended and manufacturing errors will result.
Design engineers must also be concerned with angular shifting of forces as the cutter descends through the workpiece causing previously sufficient constraints to fail to hold the workpiece adequately. There is also future-proofing to consider as the risk of a change in either machine horsepower or cutting speed could cause unexpected cutting force to be felt on the workpiece in a manner that the fixture was not originally designed for. All of these types of errors must be considered by a skilled design engineer in order to minimize product rework requirements.
Further Reading:
Dvorak, P., (1998), "Poka-yoke Designs Make Assemblies Mistakeproof", Machine Design, (March), pp. 181-4
Member discussion