Design for Manufacturing: Corners in Machined Parts
Today we will look at the economics and design considerations for using sharp corners in machined parts. We'll also look at burr removal.
Many engineers seek to prevent end-user injury by specifying that all sharp corners be removed from parts before the next step of the manufacturing process. This practice errs on the safe side; however, such a practice is not economically viable in many (if not most) situations. Breaking all sharp edges and corners adds substantial time to the manufacturing process. In addition, it also requires additional operators to compensate for the nonstandard nature of the operation. You need to also have quality checks to make sure that the step has been followed.
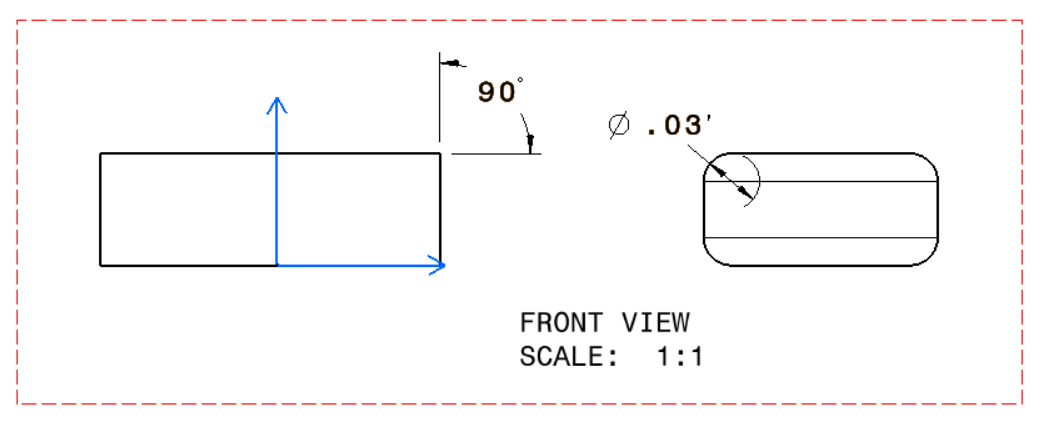
Is that necessary?
Instead of having operators take the post-processing step of deburring and corner breaking, design engineers should consider creating curves and chamfers as part of the manufacturing process so that it's accounted for in the NC programming (as shown in the CAD model above). Standard milling operations may accomplish this. However, a better alternative is incorporating it into the casting or forging processes whenever possible to reduce overall setup time. If casting is used, it is vital to ensure that flash from mold mating surfaces is not present before machining, as it may interfere with clamping or locating operations. There's nothing worse than having to file down the workpiece before putting it on the clamp.
If
While designing machined parts:
-If you believe that the build plan will require breaking sharp edges and corners
-Or if you are designing the part to have pockets
Then
(a) Instead of the build plan order to break all sharp edges and corners, consider using chamfers and curves to prevent the formation of burrs. This will move the manufacturing requirement to a CNC-controlled device rather than require a manual operation
(b) Only break sharp corners where hazards or product failures are at risk.
(c) Consider adding chamfered edges in the casting processes.
(d) Avoid the use of internal corners that lack a chamfer
This thumb rule will prevent product malfunction due to burrs causing mechanical binding. Additionally, it will prevent injury in the handling of the part due to sharp corners. It will also minimize cutter changes or secondary material removal through another process.
Member discussion